VSP G1 Process Connections
Rename to Setup and Operation Guide
Description of the process connections on the G1 and their main use cases.
Reference setup
Operating procedures
Leak tightness testing
Testing for leak tightness is an essential part of preparing the system for particle production to optimise safety and minimise unnecessary exposure to nanoparticles.
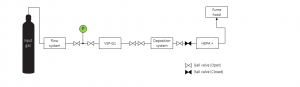
- After checking the flow connections, ensure that the pressure gauge is turned on (and functioning). Close the system (see diagram of a sample setup below), and slowly turn on the gas flow. When the system reaches +0.2 bar overpressure, switch off the gas supply. The internal pressure should remain the same. If system pressure drops more than a few millibar over the course of 10 minutes, there is a leak in the system, and you should proceed to step 2. If the system is leak tight you can proceed to "Start nanoparticle production".
- To narrow down the location of the leak, you can perform the leak test of step 1 on a sub-section of the setup (compartmentalization). In the basic setup, we use ball valves for this purpose. The schematic to the right shows a sub-section with the VSP-G1 unit (our particle source). Note that the pressure gauge must be part of the isolated sub-section. Check for leaks in the same way as step 1.
'Step 2: Partial compartmentalization of the particle source to check for leak tightness. - To resolve the leak, check the process connections within the leaking (sub-)section. Make sure the process connections are correctly made according to manufacturer specifications. Tighten the connections and/or replace the tubing wherever necessary. Leak-detecting spray may be useful to identify faulty process connections, but should not be used on the reactor assembly or base unit.
- Repeat these steps for every enclosed section (see diagram below) of the setup until the system is leak tight. If leaks persist, check the proper installation of the pressure gauge connections; contact VSParticle if you suspect a leak occurs within the reactor assembly itself.
- After resolving the leaks found in the previous steps, repeat the leak tightness test of step 1 on the whole system. If the system passes, it is ready to start nanoparticle production.
Controlled air exposure
![]() |
Warning: Small metal nanoparticles can be extremely reactive. Spark-generated particles made in high purity gases can be pyrophoric, presenting a risk of fire when suddenly exposed to air. |
Oxidation-sensitive materials may present a fire or explosion hazard when suddenly exposed to air or water. This hazard is particularly relevant when high surface area materials of non-noble metals are produced under high purity conditions.
Before opening any system containing potentially pyrophoric nanomaterials to air, passivate the particles by introducing low concentrations of O2 and/or H2O into the system. As a rule of thumb, flushing the system with unpurified gas of 99.999% (5N0) purity suffices to form an initial oxidation layer.
content neededgradually introduces small amounts of air to stabilize the system before opening
Flushing the system
Notification: Flushing the system greatly reduces the risk of nanoparticle exposure when opening the unit for any reason.
To reduce risk of operator exposure, the system should be flushed before opening. The easiest way to flush is by flowing gas with the spark switched off. The time required to flush the system depends on residence time ,
the volume of the system (operating volume of the VSP-G1 is approximetly 0.3 l), and the flow rate H2O. As a general guideline, one should flush the system for at least 9 times the residence time. With a flow rate of 1 l/min, this takes about 3 minutes.