VSP-G1 User Manual
This is the comprehensive User Manual for the VSParticle Generator One Spark Generator (VSP-G1). The Quick Start Guide is available as a quick reference for standard operation of the VSP-G1 unit.
Company | VSParticle B.V. | ![]() |
---|---|---|
Address | Oostsingel 209 2612 HL Delft The Netherlands | |
Website | vsparticle.com | |
Support e-mail | support@vsparticle.com |
Introduction
The User Manual provides instructions for the set-up, installation, operation and maintenance of a VSParticle Generator 1 ("VSP-G1") unit.
Wherever a caution symbol is affixed to the machinery, there are explanatory texts located within the manual (see this section of the detailed system description for a guide to all symbols found on the VSP-G1. ). Other important safety information located within the manual are also labelled with the caution
symbol.
You will also find conformity and warranty information at the very end of this user manual.
A Quick Start Guide is also included for faster set-up as part of the standard operating procedure. For more information regarding safety, more complex operations and troubleshooting and maintenance, refer to this manual first!
If you have any questions or concerns regarding the VSP-G1 unit you have purchased or any information within the provided user documentation, please contact us via the contact details at the top of this page.

The VSP-G1 is designed for use by researchers who want to produce inorganic nanoparticles from conductive materials for applications in fields ranging from cluster research to materials science. The VSP-G1 is a desktop spark generator that uses spark ablation technology to produce aerosol nanoparticles after a high voltage spark evaporates part of two metallic electrodes. Its design is aimed at making the production of nanoparticles as simple as possible, while giving you the flexibility to customise the system by having control over:
- particle size (1 atom to 20 nm)
- ablation rate (~0.01-100 mg/h)
- carrier gas
- electrode material
- gas flow rate (1-30 l/min)
It is also possible to customise the reactor by changing configurations from through flow (the standard configuration offered with the basic VSP-G1 unit) to cross flow, co-flow and combined configurations. The portability of the system also allows it to be integrated into a larger system for more complex operating procedures.
The VSP-G1 is designed as a continuous source of aerosolized nanoparticles for use in a controlled process system. This controlled process system typically comprises a gas source, a gas-tight system of unit operations, valves and tubing, and a gas exhaust fitted with one or more particle filters. Typical conditions in the process system are room temperature and ambient pressure. The system can be run at slight over- or under-pressure.
The closed system provides a safer production of nanoparticles and can easily be dismantled for safe transport of produced nanoparticles and for system cleaning and maintenance, which can be performed following a simple and fast protocol. The closed system design also allows you to produce high purity nanoparticles without any polluting by-products. The spark ablation process eliminates the use of any chemicals, surfactants, precursors or polymers. Without the need to rely on external materials to stabilise the produced particles, you have more flexibility to choose a suitable deposition system for the aerosol nanoparticles. The three physical principles to inmobilize the nanoparticles on a support are diffusion, impaction and electrostatic precipitation. If you have any questions or need help with the selection and/or development of a system that best fits your needs, please contact us.
For more information about the spark ablation process and possible applications, refer to the Background information section.
System and operator safety
Notification: To view a list and description of all warning labels found on the VSP-G1 unit, go to the Guide to symbols found on the VSP-G1
The risks associated with a spark generator can be divided into two categories: those associated with the machine itself, and those associated with nanoparticles. Machine-related risks are more widely regulated by international norms, such as the European conformity system required for marking certain products with the CE symbol. However, synthesized nanomaterials are relatively new and their quantum effects are still being studied, thus there are less standardized measures in place. Until more is known about nanoparticles, we apply the Precautionary Principle, treating them as potential highly toxic materials. The safety measures we employ for working with, storing and transporting nanoparticles have been drawn primarily from those designed for fine particles.
Safety of machinery
The VSP-G1 spark generator comprises general electronics (<50 V), gas connections and high voltage (6 kV), as well as moving parts. Several safety mechanisms mitigate the risk for damages and incidents related to potential equipment failure, but primary responsibility for correct and safe operation lies with you as the operator of the system. The VSP-G1 is intended for use by qualified personnel only.
Operator safety actions
You are required to ensure that:
- the reactor is correctly mounted (see setting up);
- there are no objects near the electrodes;
- process connections are correctly made (see process connections);
- the pressure in the system is limited to 1±0.2 bar absolute (see gas pressure monitoring);
- all, if any, external safety systems are functional (where applicable); and
- personal protective equipment are being used correctly (gloves, glasses, and FFP3/P3 certified filter mask).
Existing protective features
![]() |
Warning: Intentional misuse of the VSP-G1 in a manner not specified by VSParticle may impair the existing protective features. |
The VSP-G1 is equiped with an interlock system. When a failure is detected, the interlock system cuts power to the high voltage supply and the motor, shutting down particle production. There are three types of interlock.
1. Internal Interlock
During start-up and while running, the VSP-G1 the control system checks if internal systems are working properly. If any check fails an internal interlock is triggered. When the interlock cuts power, you must first fix the conditions that caused the interlock to activate before clearing the interlock state. Press and depress both dials simultaneously to clear the interlock.
2. Reactor interlock
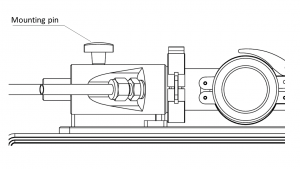
The VSP-G1 detects whether the reactor endcaps are properly mounted, using two mounting pins (see image). You must ensure that the reactor itself is correctly assembled. In short, this means that the reactor is leak tight (see the operating and maintenance guide) and that the gas inlet valve and electrode tips are free to move with a minimum clearance of 10 mm from any foreign objects (see the section on process connections and the section on flow configurations).
![]() |
Warning: Gas connections and other user-provided functions are not controlled by the interlock. An optional external interlock is available for the VSP-G1. |
3. External interlock (option)
An external interlock switch can be provided for incorporation in an external safety system. To allow operation, two pins of the interlock connector must be connected (shorted). Breaking the connection switches the system into interlock mode.
Other residual risks
Pressure. Pressure within the closed system poses a serious risk when improperly handled. Increased pressure can be caused by unintentional release of gas at high pressure, the closing of output valve while the input valve is open, clogged filters, spark obstruction, or a full deposition system. Exceeding the maximum pressure can lead to failure of the gaskets and seals, and the viewport could explode.
Non-ionizing radiation. The spark plasma emits a bright light in the visible and UV range. A viewport with a removable optical filter is included to allow visual inspection of the electrodes. Additionally, electromagnetic radiation (radio frequency) may be emitted.
Safety of nanoparticles
Because our spark generators can in principle be used to produce nanoparticles from any metal, we start from the assumption that these nanoparticles pose potential risks to the health of operators, consumers and to the environment. This manual addresses operator exposure. Consumer exposure is determined by the application in which the nanomaterials are to be used and should be evaluated on a case-by-case basis by the user. Environmental considerations should also be addressed by the operators with a life cycle analysis.
The main channels of operator exposure to nanoparticles are through (skin) absorption, ingestion and inhalation. The aerosol nature of the produced nanoparticles by the VSP-G1 system means exposure through inhalation is the main risk. The respiratory system of the human body has natural defenses in place for airborne particles such as dust, viruses and bacteria. However, nanoparticles are able to bypass most of these defenses due to their small size. For this reason, nanoparticles are treated in the same way as fine particles. More information on health and safety of nanoparticles can be found through the links at the end of this section.
Operator exposure
While the VSP-G1 unit is designed to be a closed system to maximize safety when working with nanoparticles, there will be situations in which it will be necessary to open the system, including routine maintenance activities, replacement of electrodes and filters, and sample extraction. The list below also includes some possible situations in which the operator may be inadvertently exposed to nanoparticles and a brief summary of the necessary precautions to prevent, wherever possible, such situations.
Exposure risk situation | Operator precautions |
---|---|
Gas phase exposure | An aerosol system must be leak tight from source to deposition (see section 2.1 of the operating and maintenance guide). |
Filtration | The gas exhaust should be treated with a suitable HEPA or ULPA filter. VSParticle recommends using a large capacity HEPA pre-filter, followed by an ULPA end filter. |
Dealing with pyrophoric materials | Metal nanoparticles can be extremely reactive, and can be pyrophoric (spontaneous ignition upon exposure to air).Controlled air-exposure, however, is needed before opening the system in order to passivate any reactive materials (see controlled-air exposure protocol). |
Product handling | When the system must be opened to insert or remove a substrate, methods as described in the maintenance protocols section must be followed to reduce the risk of nanoparticle exposure. |
Maintenance | Nanoparticles will collect on the surfaces inside the reactor and downstream piping. Cleaning of these surfaces presents the largest exposure risk to operators, unless they can be performed in a safe environment (e.g. a glovebox) (see system care and the operating and maintenance guide for the relevant maintenance protocols).
|
Links to more information on nanoparticles and health
- Health Significance of Nanotechnologies, a report produced by the Health Council of the Netherlands in 2006
- Nanosafety Guidelines, a set of safety recommendations by the workgroup Nanosafety of the Faculty of Applied Sciences of Delft University of Technology for working with ‘free nanostructured matter’ in research activities.
- Good practices for the use of engineered nanomaterials in a research environment, a guide describing good practices for working with engineered nanomaterials by FOM/NWO (The Netherlands Organisation for Scientific Research).
- Nanosafety Quick Check, a checklist developed based on a summary of the Nanosafety guidelines listed above.
- Ten things you should know about nanotechnology, an article available on Nanowerk website
System description
What's in the box
Congratulations on your purchase of the VSP-G1!
In the box you will find the following:
-
The VSP-G1 base unit,
-
a reactor mounted on the base unit,
-
a black viewport cover (possibly mounted on the reactor),
-
a reactor mount plate,
-
and a power supply cable
You will also find a Quick Start Guide for daily operation and a reference card for working with nanoparticles in the lab. The reference card is also available online as part of the Quick Start Guide. If there's anything missing or looks damaged, contact us immediately at support@vsparticle.com or using the contact details at the top of this page! A damaged power supply cable may temporarily be replaced by a similar cable, but ensure it has a functional protective earthing terminal.
Detailed system description
A visual reference and detailed description of the components that are part of the VSP-G1 system is provided on the Detailed System Description page. This includes a full reference of the warning labels and symbols found on the machine.
Setting up
Setting up the base unit
Mounting the reactor assembly
When shipped, the reactor assembly is attached to the transport plate in the packaging. The electrodes have already been installed. In the case you want to replace the electrodes, please see the electrode replacement protocol in the operating and maintenance guide.
To confirm that the reactor assembly is correctly assembled, use a digital multimeter (DMM) to measure the resistance between the reactor chamber and the ground point on the back of the system. The resistance should be <0.1 Ohm (keep in mind that the leads in a typical handheld DMM can have a resistance as high as 0.5 Ohm).
Building a basic setup
Your particular deposition requirements and research needs will result in a system setup that is different from others. In all cases, however, the following requirements help ensure that the system works efficiently and safely:
- Use correctly rated tools and components
- Apply compartmentalisation of the reactor and the deposition system;
- Use a gas pressure monitoring tool;
- Use a safe exhaust (fume hood with HEPA+ filters, for example) for the outflowing gas; and
- Perform regular leak checks.

The following basic operating procedure is for the simple setup pictured below, which comprises several operating units: a gas source and flow system; a particle source (the VSP-G1 unit); a pressure gauge; a deposition system; and exhaust filters. To complete the setup, the units are connected with tubes, piping, fittings, valves and so on. The ball valves () in this setup help compartmentalize the overall system for leak testing and for safe disconnection. Each setup will be different, depending on your individual needs, but the concepts described here should generally be valid.
To reduce particle losses, please take the following guidelines into account:
- Keep the tubing length between particle source and deposition system as short as possible to reduce diffusive losses.
- Use conductive tubing (metal or conductive polymer (electrostatic dissipative tubing) in particle carrying lines to reduce electrostatic losses.
- Do not use flow controllers (e.g. needle valves, mass flow controller) in particle lines, as particles will clog up the controller.
- Usually the controller can be placed in another (particle free) line, or downstream of the deposition system, behind a filter.
- If flow control is absolutely needed in a particle line, use an orifice.
- Avoid constrictions that can function as a particle trap. I particular:
- Use ball valves with a wide bore.
- Avoid fibers and meshes.
Building a setup takes three steps:
- Design/draw/sketch your flow diagram, including sensors, valves and filters.
- Assemble the VSP-G1 (see Assembling the system
- Assemble the rest of the setup according to your flow diagram.
- Check the system for leak tightness and make adjustments if necessary. (See Checking for leaks.)
Process connections
Use only tubing and components rated for the operating conditions of the system. When using quick-connect fittings and other systems that do not require tools, ensure that the system is protected against accidental opening (e.g. clamps, latches and/or signs). Different technologies can be used to connect tubing and the other components. The process connections must be made according to the fitting vendor's specifications. The VSP-G1 comes equipped with Swagelok® fittings.
Compartmentalisation
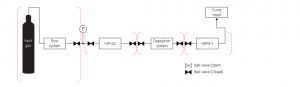
For safety reasons, we recommend compartmentalisation of every unit within the setup that regularly opens up to the atmosphere to allow for easy dismantling in a safe manner. In the setup described here, we use two valves on both sides of the deposition chamber which allows us to easily seal off both the reactor and the rest of the setup. When the deposition chamber is removed, it can be safely transported to a safe working location, such as a fumehood or glovebox, in order to take out the sample. Meanwhile, the rest of the setup, which often contains a significant amount of nanomaterial, remains safely sealed.
Gas pressure monitoring
The internal pressure should not exceed +1.2 bar or there is an increased risk of failure of the gaskets and/or seals in the reactor, causing leaks and risk of nanoparticle exposure. A build-up of pressure within the system might be an indicator of obstruction, either within the reactor, the deposition system or in the filtration system. Ideally, a pressure sensor at the reactor inlet is used to automatically switch off the gas supply. Stop spark production and gas flow immediately when pressure reaches +1.2 bar to determine the source of obstruction and resolve the issue. See System care for cleaning procedures.
Flow configurations
The VSP-G1 has multiple inlets and outlets, that allow the user to modify the flow profile around the spark gap. Configurations usually have a single outlet for the particles, but can have a single or multiple inlets. Possible reasons to modify the flow configuration are to change the dilution rate in the gap, or to apply a sheath or dilution gas. Particular attention must be taken if the hollow electrode is used as the only outlet: During the startup sequence, the VSP-G1 lets the electrodes touch, obstructing the outlet flow.
![]() |
Warning: When using the hollow electrode as the only outlet, be sure not to mount a solid electrode tip. |
Exhaust
The gas exhaust should be treated with a suitable HEPA or ULPA filter. VSParticle recommends using a large capacity HEPA pre-filter, followed by an ULPA end filter. Replace the pre-filter before the end-filter is filled. The filtered exhaust should not be vented directly into a workspace; vent the outflowing gas through a fume hood or other suitable (non-recirculating) ventilation exhaust.
Checking for leaks
Refer to the operating and maintenance guide for information on how to perform a leak test on the system.
Electronic connections
Grounding the system
The spark generator uses the ground from the mains plug for safety. Use only certified cables and properly wired wall outlets. The separate functional earth terminal on the back of the base unit (#21 in the base unit back diagram above) is internally connected to the mains connector ground, and should be independently connected to the protective ground in the case a recommended mains power supply plug is unavailable.
Power supply connection
After assembling the base unit and reactor, plug in the provided mains cable into the mains inlet and connect the VSP-G1 to a mains outlet (110-230VAC).
Communication The VSP-G1 comprises a female 9-pin sub-D connector.
Pin | Purpose |
---|---|
2 | Tx (output) |
3 | Rx (input) |
5 | Common |
Unassigned pins are not connected. |
The VSP-G1 can be remotely controlled using RS232 over the sub-D connector. Please refer to the section 5.1.2 on remote controlled operation.
Operating the system
![]() |
Warning: Do not handle or open the system while particles are being generated and while gas is flowing. |
Controls
Manual control
The VSP-G1 can be controlled directly from the front panel using the two dials and the button on the left hand side. The two dials on the front panel can be pressed to select a function, such as changing a set point. In general, the dials can be used to change the value shown directly above it on the display by pressing the dial and then rotating it to change the associated value. Another press of the dial then locks or confirms the value. The button on the left hand side of the front panel is used solely to toggle sparking. Refer to the controls and indicators section of the detailed system description for additional information. This section further describes the key functions of the dials and button in various states of operation of the VSP-G1.
Starting the alignment sequence
When powering up the device, the message "Begin electrode alignment" appears on the display. Confirm no carrier gas is flowing and that the gas inlet is free to move, then confirm by pressing the right hand dial.
Changing the charging current and/or gap voltage set point
This can be done during sparking and when the "Ready to spark" message appears on the display. Press the dial underneath the value you wish to change and then rotate the dial to change the set point. Press the dial again or leave it untouched for 2 seconds to confirm the value.
Start/stop sparking
Sparking can only be initiated when the "Ready to spark" message is shown on the display. Press the button to start sparking. When sparking, another press of the button will return the system to the idle "Ready to spark" mode.
When the "Ready to spark" message is displayed, press and release both dials simultaneously to access the menu. By turning the right hand dial, you can browse the menu options. Press the right hand dial to confirm or alter a menu setting. When altering a setting, press the right hand dial again to confirm the value. Pressing the left hand dial exits the menu and returns the system to the "Ready to spark" mode.
Remote controlled operation
The VSP-G1 can be controlled remotely via the 9 pin D-SUB connector at the back of the system. The remote control structure allows for changing set points and reading the status of the device. It does not allow access to the settings menu and cannot initiate the electrode alignment procedure during start up. A full discussion of the command structure, functions and limitations can be found in the Remote control guide.
Basic operating procedure
An abridged form of this section is also available as a Quick Start Guide, including a themed version for printing.
Preparation
- Ensure that the system is leak tight.
- Power up all systems, includeing the VSP-G1 using the mains switch on the back panel near the power connector. Ensure the power cable is properly fitted and powered.
- When the "Start electrode alignment?" message appears on the display, press and release the right hand dial on the front panel to start the alignment sequence.
- Wait for the alignment procedure to complete. Several messages appear on the display during the sequence to indicate activity. The integrated LED on the button will blink during the entire sequence and stays on once completed.
- Ensure that the path to the exhaust is clear and all required valves are open.
- Start the carrier gas flow.
- Monitor the pressure to ensure it is within the required range (0.8-1.2 bar(a)).
Notification: Carrier gas selection: The VSP-G1 supports Ar and N2 as carrier gases. The system needs to be configured for the carrier gas that you use. Follow the instructions in the operating and maintenance guide to verify the right carrier gas setting is selected. If set incorrectly, the spark will be unstable or very slow in reaching the desired setpoints.
Start and stop nanoparticle production
The set points for charging current (frequency control) and gap voltage may be altered when the system displays the "Ready to spark" message and when the system is sparking. The set points are controlled by the two dials on the front panel. The left hand dial is associated with the gap voltage setpoint while the right hand dial controls the charging current. Higher voltage and current generally lead to larger particles.To change a setpoint:
- Press and release the corresponding dial. The unit of the associated value (e.g. kV or mA) will start blinking indicating the value is unlocked.
- Rotate the dial to set the desired value.
- Press and release the dial once more or wait 2 seconds to lock the value.
To start sparking, press and release the button on the left hand side of the front panel. The indicator LED around the button will change from solid to blinking red, indicating the machine is in operation. To stop sparking, press and release the button once more. This will return the system to the "Ready to spark" mode. It's possible to adjust the particle output by changing the voltage and current settings.
We recommend leaving the system to equilibrate/stabilise for 15-30 minutes, depending on your specific needs. This time allows the system to warm up, and the surface of the electrode tips to be refreshed and removing, if any, surface oxides.
Shutting down
- Make sure the system is in "Ready to spark" mode.
- Press and release both dials simultaneously to enter the menu. The option to shut down the system is selected upon reaching the menu.
- Press and release the right hand dial to confirm shutdown.
- Wait for the message "Please power off" to appear
- Set the mains switch near the power cable at the back of the system to the 0 position.
Opening the system
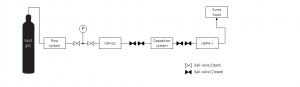
Common reasons to open the system are to place or remove a sample/substrate, to clean the reactor, or to change electrodes. To reduce the risk of exposure when handling non-immobilized nanomaterials, it's recommended to open the system in a controlled working environment. If the deposition chamber is not equipped with sufficient protective measures, it can be convenient to move the deposition chamber itself to a fume-hood or glovebox (see image).
Steps required before opening the system:
- Stop particle production.
- Flush the system (see the corresponding section in the operating and maintenance guide).
- Stop the gas flow.
- Take out your sample following the procedure for your deposition system, taking the necessary precautions to prevent/reduce exposure to nanoparticles. Pay special attention when handling potentially pyrophoric nanoparticles.
System care
The system requires no regular maintenance by the end user, but cleaning the reactor periodically is recommended, especially after a change of electrode material. To prevent exposure to nanoparticles and to ensure safe and efficient cleaning, guidelines are set out in the operating and maintenance guide. The procedure to replace electrodes is also discussed there.
When to clean the reactor and replace the filter(s)
Clean the reactor whenever you replace the electrodes, the reactor is dirty, or after 100-1000 hours of operation (which in turn depends on your operating conditions: if making more particles, clean more often). If higher settings are needed to maintain a spark flow, it is possible that the reactor needs to be cleaned to prevent spark obstruction which can possibly lead to spark misfiring within the reactor system. If the pressure within the system increases even with the valves open, it is possible that the filter is full and needs to be replaced. Refer to the operating and maintenance guide for more information.
Safe handling and storage
The VSP-G1 is a scientific instrument, and must be handled with care. This section provides general guidelines on how to safely handle and store the system. Detailed methods are described in the operating and maintenance guide.
![]() |
Warning: Flush the system before opening the system. |
Disassembly
The base unit with reactor installed has a combined weight of 22kg. For general handling, e.g. when assembling a setup, the reactor is conveniently be transported separately from the base unit. A mount plate / transport tool is provided for this purpose. See unmounting the reactor assembly of the operating and maintenance guide.
General disposal guidelines
Disposal of nanomaterials
Label and dispose cleaning materials contaminated with nanomaterials according to local rules and regulations. See also Filter replacement and disassembling and cleaning the reactor.
Retiring the VSP-G1
Local regulations and practices apply for disposal of electronic equipment. If the VSP-G1 has reached end of life, please contact VSParticle at support@vsparticle.com for recommendations on how to dispose of the system.
Transportation, packaging and storage
VSParticle recommends using the original packaging for transportation and shipping. Be sure to clean the reactor before shipping the reactor. The system should also be cleaned if it is not to be used for a longer period of time.
When shipping the system to VSParticle or one of it's representatives for any reason, return authorization (RA) is required. Contact your distributor. For systems supported by VSParticle, an RA form can be requested by sending an e-mail to support@vsparticle.com.
Troubleshooting
There are several possible issues that may arise during normal operation of the VSP-G1. The most common scenarios and errors are listed below.
Unstable operation
In some scenarios, unstable operation of the spark (wild fluctuations of the gap voltage, intermittent sparking and/or the system is slow to reach its set point) may be encountered. There are several causes for such instability to occur:
- Glow mode is active. In this case, a weak arc is observed between both electrodes and the gap voltage drops suddenly. Please refer to the glow mode section below.
- The carrier gas selected on the system differs from the carrier gas being used. Symptoms include wild fluctuations around the intended gap voltage set point and the motor in the system can be heard adjusting the gap all the time. Alternatively, the system may be very slow to reach the intended set point. To correct the issue, ensure the correct carrier gas is selected by following the instructions in the operating and maintenance guide.
- Oxidation of the electrode material has occurred. This can result in fluctuations and/or intermittent sparking until the oxidised material has been ablated. To resolve this issue more quickly, increase the spark frequency by increasing the charging current set point and optionally the gap voltage (to avoid glow mode).
Glow mode
Occasionally the spark voltage drops suddenly, and a weak arc may be seen between the two electrodes. This is caused by a too high charging current. If this occurs directly after changing the spark voltage or spark current set point, the control system in the VSP-G1 will likely correct the situation. If not, the chosen set point cannot be maintained in spark mode. Increase the spark voltage or decrease the operating current to correct the situation.
Interlock errors
Message on display | Cause | Resolution |
---|---|---|
Interlock err. 7 | Motor controller failure | The motor controller reports a failure. This can be due to:
|
Interlock Error 8 | Broken interlock switch | One of the interlock switches is broken or has a broken connection. Verify both reactor mounting pins are properly secured and that the reactor is properly mounted on the base unit. Press both dials to clear the error and try again. If the error persists, contact VSParticle. |
Interlock Error 9 | Open interlock switch | One or more interlock switches are in the open state. Verify both reactor mounting pins are properly secured and that the reactor is properly mounted on the base unit. Press both dials to clear the error and try again. |
If you encounter any interlock error other than the ones listed above, please try to clear the interlock by pressing and releasing both dials and/or switch the VSP-G1 off and on again. If the error persists, please contact VSParticle via support@vsparticle.com.
Electrode alignment
When the VSP-G1 starts aligning electrodes during start-up, several sounds may be heard:
- Quick hammering. This occurs occasionally when the electrode is in an unusual position (e.g. after maintenance/cleaning of the reactor has been performed) and cannot move in the expected direction. This is normal. The sounds should not last more than a second and the system corrects itself and completes the alignment procedure. If the sounds persist for more than a few seconds, switch off the VSP-G1 using the main power switch at the back. Follow the instructions for a blocked motor found under the Interlock err. 7 entry of the interlock errors section above.
- Clicks. These occur at the boundaries of the adjustment range and are no cause for concern.
- Vibrations or rattling. This can occur when there is tension on the gas inlet of the left end cap, restricting free movement or due to wear of the transmission. Check that the gas inlet is free to move. If these sounds occur regularly, contact VSParticle.
When the electrode alignment sequence fails, this is displayed as Interlock err. 7. Refer to the interlock error section above for possible resolutions.
When to contact VSParticle
- If the system keeps reverting to interlock without apparent reason.
- If sparks can be heard or seen in any location other than between the electrode tips.
Accessories and replacement parts
Use only VSParticle approved parts. All parts related to the reactor assembly must be examined and/or supplied by VSParticle. Contact us for more information.
Specifications of replaceable parts that can be obtained by other suppliers:
Fuses - The fuse holder accepts 5x20mm T2.5A/250V fuses.
Power cable - IEC-60320 compliant with C13 connector,
RS-232 cable - any standard (straight) RS-232 cable is suitable.
Appendices
VSP-G1 technical specifications
Additional information about the VSP-G1 operating window, electrical specifications and output can be found on the Technical Specifications page.