VSP-G1 Operating and maintenance guide
General
This guide contains a selection of operating and maintenance procedures. The VSP-G1 does not need much maintenance, but several procedures ensure good operation through its working life.
User maintenance on the base unit is limited to periodic cleaning and fuse replacement. The base unit should be cleaned with a cloth or wipe moistened with IPA, ethanol or water. Do not spill liquids onto the base unit.
Regular use maintenance includes cleaning the reactor by removing generated particles left in the reactor, and the replacement of electrodes. of the reactor is described in section Reactor assembly. The windows of the viewport and viewport cover and the electrical contacts in the reactor ends and the base unit are fragile, and requires special care (see Cleaning the viewport).
Operating procedures
Leak testing
Testing for leak tightness is an essential part of preparing the system for particle production to optimise safety and minimise unnecessary exposure to nanoparticles. The following procedure is provided for reference. Other leak testing methods may be applied as well.
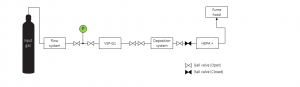
- After checking the flow connections, ensure that the pressure gauge is turned on (and functioning). Close the system (see diagram), and slowly turn on the gas flow. When the system reaches +0.2 bar overpressure, switch off the gas supply. The internal pressure should remain the same. If system pressure drops more than a few millibar over the course of 10 minutes, there is a significant leak in the system, and you should proceed to step 2. If the system is leak tight you can proceed with the basic operating procedure in the user manual to start the system.
'Step 2: Partial compartmentalization of the particle source to check for leak tightness. - To narrow down the location of a leak, you can perform the leak test of step 1 on a sub-section of the setup (compartmentalization). In the basic setup, we use ball valves for this purpose. The schematic to the right shows a sub-section with the VSP-G1 unit (our particle source). Note that the pressure gauge must be part of the isolated sub-section. Check for leaks in the same way as step 1.
- To resolve the leak, check the process connections within the leaking (sub-)section. Make sure the process connections are correctly made according to manufacturer specifications. Tighten the connections and/or replace the tubing wherever necessary. Leak-detecting spray may be useful to identify faulty process connections, but should not be used on the reactor assembly or base unit.
- Repeat these steps for every enclosed section (see diagram below) of the setup until the system is leak tight. If leaks persist, check the proper installation of the pressure gauge connections; contact VSParticle if you suspect a leak occurs within the reactor assembly itself.
- After resolving the leaks found in the previous steps, repeat the leak tightness test of step 1 on the whole system. If the system passes, it is ready to start following the basic operating procedure in the user manual.
Controlled air exposure
![]() |
Warning: Small metal nanoparticles can be extremely reactive. Spark-generated particles made in high purity gases can be pyrophoric, presenting a risk of fire when suddenly exposed to air. |
Oxidation-sensitive materials may present a fire or explosion hazard when suddenly exposed to air or water. This hazard is particularly relevant when high surface area materials of non-noble metals are produced under high purity conditions.
Before opening any system containing potentially pyrophoric nanomaterials to air, passivate the particles by introducing low (<1%) concentrations of O2 and/or H2O into the system. As a rule of thumb, flushing the system with unpurified gas of 99.999% (5N0) purity suffices to form an initial oxidation layer. Alternatively, a pinhole leak can be used to introduce air into the system.
Flushing the system
Notification: Flushing the system greatly reduces the risk of nanoparticle exposure when opening the unit for any reason.
To reduce risk of operator exposure, the system should be flushed before opening. The easiest way to flush is by flowing clean gas with the spark switched off. Alternatively, the system can be evacuated before opening. Note that in both cases, a significant fraction of the particles will be collected on the reactor and tubing walls, and may become resuspended.
Flushing, method 1
The time required to flush the system depends on residence time ,
the volume of the system (operating volume of the VSP-G1 is approximetly 0.3 l), and the flow rate H2O. As a general guideline, one should flush the system for at least 9 times the residence time. With a flow rate of 1 l/min, this takes about 3 minutes.
Flushing, method 2
Evacuate the system to <1 mbar. Refill slowly (to avoid resuspending particles). Repeat 2x.
Reactor assembly
Assembling the reactor
Mounting the reactor assembly
Please follow the instructions in the setting up section of the user manual once the reactor has been assembled on the transport plate.
Unmounting the reactor assembly
- Switch off spark and flush the system.
- Stop gas flow and depressurize.
- Select "Shut down" from the menu and shut down the system with the mains switch.
- Unscrew the mounting pins.
- Lift the reactor and transfer it mount plate. Secure the reactor to the mount plate with the mounting pins.
Disassembling and cleaning the reactor
- Move mounting plate with the reactor to an environment where risk of particle exposure is limited, such as a fume hood or glove box.
- Open and remove the right clamp. Remove the right end-cap and O-right by sliding them to the right.
- Gently wipe the surfaces of the right endcap and the O-ring with a cleaning cloth/wipe, moistened with ethanol, water, or IPA. Use a moistened cotton tip to clean inside tubing.
- Open and remove the left clamp. Remove the reactor housing and O-ring by sliding them to the right.
- Gently wipe the surfaces of the reactor housing, electrode, left endcap and the O-ring with a cleaning cloth/wipe, moistened with ethanol, water, or IPA. Use a moistened cotton tip to clean inside tubing. For cleaning the viewport, see Cleaning the viewport.
- Dry the endcaps, reactor housing and O-rings using filtered pressurized air or a dry cloth. No visible trace of solvent should remain.
- Assemble the reactor.
Notification: Label and dispose cleaning materials contaminated with nanomaterials according to local rules and regulations.
Replacing electrodes
- Switch off spark and flush the system.
- Select "Change electrodes" in the menu, and shut down the system with the mains switch.
- Unmount the reactor.
- Disassemble and clean the reactor.
- Unscrew the cleaned electrode tips.
- Screw in the replacement electrode tips.
- Assemble and mount the reactor by following the instructions in the setting up section of the user manual.
Changing carrier gas
The VSP-G1 supports Ar and N2 as carrier gas. It is essential that the type of carrier gas is specified correctly to avoid slow performance of the gap control or instability of the system. To select the correct carrier gas:
- From the "Ready to spark" mode, go to the menu by pressing and releasing both dials on the front panel simultaneously.
- Turn the right hand dial until the "SET CARRIER GAS:" option appears on the display. The currently selected carrier gas is displayed below.
- To change the carrier gas, press and release the right hand dial. The carrier gas selection will now blink.
- Turn the right hand dial to select another carrier gas.
- Press and release the right hand dial to set the carrier gas.
- Press and release the left hand dial to exit the menu. The VSP-G1 is now immediately ready to start sparking with the new carrier gas settings.
Periodic maintenance
It is necessary to periodically clean the left insulator, which is normally left in the fully retracted position when removing the endcap for any reason already described in this manual. If there is too much particle build-up in the reactor there is a risk of electrical damage to the VSP-G1 unit. To clean the hidden insulator surface, the electrode position can be adjusted starting the alignment sequence, and switching off the base unit without selecting shut down in the menu. Ensure that all surfaces are dry before reassembly.
To clean the base unit, use a cloth moistened with water, ethanol or isopropyl alcohol.
Cleaning the viewport
![]() |
Warning: The inner side of the viewport is coated with a delicate coating that scratches easily. Wear lint-free or surgical rubber gloves when handling. Do not touch the inner surface. |
Notification: The provided viewport clamp reduces operator exposure risk by preventing unauthorized opening of the viewport. Do not use the quick-release clamps for the viewport.
- Unmount the reactor, and place the mount tool with reactor on a working surface.
- Remove the viewport cover with a gentle twisting motion.
- Use a 8 mm wrench to open the viewport clamp.
- Carefully remove the viewport.
- Clean the inner surface of the viewport window:
- Remove large particles with filtered pressurized air.
- Remove light smudges by wiping very gently with a lint free optical wipe moistened with IPA
- If the window shows serious marks and/or contamination, contact VSParticle
- Place the O-ring and viewport cover on the reactor housing, and place the viewport clamp. Tighten with a torque wrench. Do not overtighten.
Filter replacement
Notification: The VSP-G1 does not contain any user serviceable filters. This section covers filters used in the overall system, as described in the exhaust section of the user manual.
This procedure is entirely dependent on your particular setup and deposition system, but we recommend the use of a HEPA filter or one of higher quality/filtration efficiency. Particle filters are characterized by a drop in filtration efficiency for particles between approximately 100 and 300 nm. For particles smaller than 20nm as generated by the spark generator, filter efficiency is typically >99.99%. In heavy use situations, a high capacity (HEPA) pre-filter can be used to protect a more expensive end filter.
Dispose used filters according to your local disposal guidelines and any particular requirements outlined by the filtration system you choose for your setup. At a minimum, the filters should sealed and labelled in a sturdy plastic bag.
Fuse replacement
Shut down the system, turn off the mains switch, and unplug the cable from the base unit. The fuseholder is located on the back of the base unit between the mains switch and the mains supply plug, accepts 5x20mm T2.5A/250V fuses.