VSP-G1 Background information: Difference between revisions
T.coppejans (talk | contribs) (Created page with "=== Theoretical background === ====Overview of nanoparticle research==== Nanoparticles are unique in the way that their size changes their material properties. The properties...") |
T.coppejans (talk | contribs) |
||
Line 1: | Line 1: | ||
=== Lifecycle analysis === | |||
The waste of the spark generator consists of the carrier gas plus any nanoparticles not deposited on the substrate but picked up when cleaning the reactor surfaces and the pre- and end-filters. These materials should be pooled, preferably separated by the elements in the waste, in order to recycle the metals. The carrier gases are typically inert Ar and N<sub>2</sub>, which can be vented (e.g. through a fumehood). If other carrier gases are used (toxic, greenhouse, etc), capture or post-treatment should be used to conform to general industry or laboratory standards on gas use. | |||
Life cycle analysis for the end product should be evaluated by the operators on a case-by-case basis. | |||
=== Theoretical background === | === Theoretical background === | ||
====Overview of nanoparticle research==== | ====Overview of nanoparticle research==== |
Revision as of 16:23, 22 March 2017
Lifecycle analysis
The waste of the spark generator consists of the carrier gas plus any nanoparticles not deposited on the substrate but picked up when cleaning the reactor surfaces and the pre- and end-filters. These materials should be pooled, preferably separated by the elements in the waste, in order to recycle the metals. The carrier gases are typically inert Ar and N2, which can be vented (e.g. through a fumehood). If other carrier gases are used (toxic, greenhouse, etc), capture or post-treatment should be used to conform to general industry or laboratory standards on gas use.
Life cycle analysis for the end product should be evaluated by the operators on a case-by-case basis.
Theoretical background
Overview of nanoparticle research
Nanoparticles are unique in the way that their size changes their material properties. The properties can change due to quantum effects, or simply because their large surface area increases reactivity. As we continue to understand more about the quantum properties of nanoparticles, we can begin to appreciate the possibly endless applications of nanoparticles. If we look at the scientific literature published in the last five years, there are six major areas of scientific study focusing on the application of nanoparticles (FOOTNOTE: compiled using the Scopus database https://www.scopus.com/): catalysis, sensors, electronics, coatings, energy and health. The highest number of publications are from the fields of catalysis, health and energy, with energy research containing the most subfields. Another area not as widely studied as the six mentioned above, (but has interesting potential), includes the application of nanoparticles in lubricants to improve lubricant performance.
The subfields of nanoparticle application research within the six areas and their possible industrial [commercial?] applications include:
Field | Subfield | Possible applications |
---|---|---|
Catalysis | New catalysts | Atomic mixing enables the creation of completely new alloys and materials with improved catalytic activity. |
Impregnation of supports | Spark discharge can be used to impregnate nanoparticle-sized catalytic support, which greatly improves surface area and has already been applied in catalytic converters in cars. | |
Sensors | DNA/RNA detection | By attaching small pieces of DNA or RNA to a MNP, the complementary piece of that DNA can be detected, which is useful in medical diagnostics or genetic modification. |
Gas sensors | Sensors can be made much more sensitive by using MNP's and can be applied to many gases. | |
Bio-sensors | MNP's can be used to improve bio-sensors that detect organic compounds. | |
Electronics | Printed circuits | MNP's can be deposited in a pattern or lines to create electronic circuits. |
Flexible electronics | The circuits are thin enough to be flexible and can be deposited on any surface, even fabrics. | |
Photodetectors | ( ) ask Joost to expand on this...? | |
Coatings | Functional coatings | Surfaces could be modified with MNP's to create a transparent, functional coating, which could produce energy, be self-cleaning or be hydrophobic. |
Anti-corrosion coatings | Depositing layers of AlO makes the underlying metal more oxidation resistant. | |
Energy | Fuel cells | Integrating Platinum or Palladium NP's as catalysts in fuel cells could make them more efficient. |
Solar cells | Using quantumdots in solarcells could make efficiencies possible above 40%. | |
Water splitting | Gold MNP's can improve photochemical water splitting. | |
Hydrogen storage | Magnesium nanoparticles are a promising candidate for efficient Hydrogen storage. | |
Lithium-ion batteries | Using NP's in batteries improves charging time and the lifetime of the battery. | |
Health | Anti-microbial coatings | Incorporating silver MNP's in fabrics makes the fabric anti-bacterial, a procedure that is relatively easy to do with spark discharge. |
Cancer treatment | MNP's are being used in research for new cancer drugs and to improve chemotherapy. How? Be a little more specific | |
In-vivo imaging | NP's can be used for medical imaging, as contrasting agents in MRI or other techniques. | |
Toxicology | Testing the toxicology of nanoparticles can be made faster and easier using spark discharge. |
Above table based on data search using Scopus.
Overview of gas phase nanoparticle production
Nanoparticles come in different forms, from dendrimers and composites to carbon-based and metal-based materials, and can be stored in different media, from films to colloids and aerosols. There are different methods based on the form of nanoparticles desired. Meuller and his colleagues summarized the methods of gas phase production of nanoparticles in their review of spark discharge generators (2012), which included flame spray pyrolysis, spray protolysis, electrospray, evaporation/condensation of material and aerosol generation by spark discharge. All methods except for electrospray produce high purity nanoparticles with narrow size distribution at a high production rate. The well-proven electrospray method, which deposits the colloidal particles in a controlled homogeneous manner that minimizes residues where still present, has been in use for a longer time compared to other methods with readily available materials on the market. Both spray protolysis and spark discharge methods are simple and fast. The evaporation/condensation method offers detailed control over deposition parameters. The spark discharge method can easily be scaled up, using more sparks per time or multiple sparks in parallel. The flame spray pyrolysis, evaporation/condensation of material and spark discharge methods all require higher amounts of energy. In the case of the evaporation/condensation of materials, the time and energy consumption required limit the overall operation time of the generation system. The spray protolysis and electrospray methods require the use of precursors and solutes, potentially contaminating the process. Flame spray pyrolysis requires postprocessing for the production of non-oxide nanoparticles. Depending on the desired end product or process, each method has their own set of advantages and disadvantages.
Production method | Summary |
---|---|
Flame spray pyrolysis | High purity nanoparticles and narrow size distribution at a high production rate. Requires higher amounts of energy and precursors in most cases need to have physical properties that are not too dissimilar. Postprocessing is most often required for the production of non-oxide nanoparticles. |
Spray protolysis | A simple and fast process for the production of high purity nanoparticles and narrow size distribution at a high production rate. Precursors and solutes are necessary, which potentially contaminate the process. |
Electrospray | Deposition of colloidal particles in a controlled homogeneous manner that minimizes residues where still present. Precursors and solutes are necessary, which potentially contaminate the process. |
Evaporation/condensation of material | Good yield and offers detailed control over deposition parameters. Energy consumption and the longer heat up and cool down times of the furnace limit the overall operation time of the generation system. |
Aerosol generation by spark discharge | Simple method that provides a reasonable yield of high purity nanoparticles with less contaminants involved in a process that can be easily scaled up. Requires higher amounts of energy. |
Table based on Meuller, et al. (2012): 1256-7.
Aerosol generation by spark discharge
From the perspective of researchers interested in studying material properties, the spark discharge method provides nanoparticles in a fast, simple manner that eliminates any other contaminants that prevent the study of the pure quantum properties of the nanoparticles. From an industrial (commercial) perspective, the spark discharge method provides a way of producing and depositing nanoparticles directly onto the final product, avoiding issues of transportation and stabilization of mass-produced nanoparticles.
The spark discharge process (based on Meuller et al., 2012)
ASK TOBIAS FOR CLARIFICATION ON THE PROCESS AND CLEAN THIS UP
The spark discharge generator is composed of two primary components - the chamber that houses the electrodes and the electric circuit required to control the spark generation.
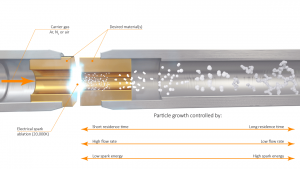
need to edit the graphic to include labels for the different sizes of the coalesced particles The electrodes are mounted with a gap in between them. A certain amount of electricity (voltage) is required to create a high electric field that accelerate the electrons and cations (on the surface of one electrode?), causing electrons to be knocked out and creating a chain reaction that results in the formation of a plasma channel that is able to conduct the electricity between the two electrodes. The resulting sparks cross the gap from one electrode to another, evaporating the electrodes into a vapor of gaseous electrode material. As the vapor forms, the resulting material stabilises itself due to adiabatic expansion (Hinds, 1982; Tabrizi et al., 2009), radiation, and thermal conduction below the evaporation temperature (Tabrizi et al., 2009). In the tight space around the plasma channel, the particles coalesce into larger forms. However, as the temperature of the particles cools, their size becomes more stable. This is where the use of the carrier gas becomes important. The role of the carrier gas is not only to cool the particles (and thus controlling their size), the gas also keeps the reactor chamber cool and moves the particles away from the plasma channel. The quantum properties of the new particles can cause them to react with the carrier gas, which means the type of carrier gas used is also relevant. Using an inert gas helps maintain a stable atmosphere for the particles during formation and in "storage".
In research applications in which the material properties of the nanoparticles are of primary interest, the produced nanoparticles are stored in a substrate (such as? paper? etc) designed to the research needs of the scientists. For industrial applications, however, maintaining the material properties of the nanoparticles usually requires their deposition directly where they are needed within the production process. An example of this would be creating a product that is self-powering by creating nanoparticles with photovoltaic properties and spraying them onto the surface of the product as the particles are produced.
Research using spark discharge technology
Applications of spark discharge technology in various fields. Give examples, do not be exhaustive.
History of the spark discharge technology
(how does our machine improve on the original design?)
(ask TC how to mirror the Technology page of VSP website)
The technology behind VSP-G1
References
What citation format do we use here? A compiled list of literature applicable to VSP-G1's technology and applications.
Health Council of the Netherlands. Health significance of nanotechnologies. The Hague: Health Council of the Netherlands, 2006; publication no. 2006/06E. Available online. Set up to open in new window
Hinds, W.C. Aerosol Technology: Properties, Behaviour, and Measurements of Airborne Particles. Wiley & Sons, New York, 1982.
Hoeneveld, D. et al. Nanosafety Guidelines. Delft University of Technology: NanoSafety workgroup of the Faculty of Applied Sciences, 2008. Available as downloaded document. Set up to open in new window
Meuller, B. O. et al. Review of Spark Discharge Generators for Production of Nanoparticle Aerosols. Aerosol Science and Technology, 2012. doi: 10.1080/02786826.2012.705448.
Tabrizi, N.S. et al. Generation of nanoparticles by spark discharge. J. Nanopart. Res., 2009; 11:315-332.
MISC TEXT
From research to commercial applications This might not be a good place for this... move this to website
There are few applications imaginable where a single, free nanoparticle would be relevant. The value of nanoparticles lies in the quantum properties that enhance more tangible products, such as improving drug delivery methods at the cellular level or creating more efficient solar cells. However, the same quantum properties that makes these particles interesting present a drawback at the industrial level - not much is known about the quantum properties. Some nanomaterials are perfectly safe, but other nanomaterials might be even more toxic. Currently there is no method of predicting whether or not a specific particle (size, shape, composition) would present a health hazard.
Moreover, handling of nanoparticles is not trivial. It's very difficult, if not impossible, to separate two particles once they touch without the use of surfactants or other chemistry. Most nanomaterials are desired for their purity and particular deposition state, thus it is cost-ineffective and time-consuming to produce nanomaterials, collect them for shipment, separate them, and incorporate them into a product in yet another process, rather than to produce the nanoparticles in-line and deposit them directly where they are needed. The VSP-G2 is being designed for direct integration into the industrial production process. Are there other nanoparticle "generators" that can be directly integrated into the industrial production process?